spaces that last generations

OPEN LOVE LETTER TO ALL LSC PRACTITIONERS
all of you
are my heroes
lets bring this phenomenal option
to the world
and promote
a better way of building
lets collaborate
Light Straw Clay insulation wall systems:
clay + straw + and wood and nothing else
SOUNDPROOF | FIRE PROOF ? | MOLD INHIBITOR | HUMIDITY REGULATOR MAGNETICALLY BENEFICIAL | ALLERGEN FREE | LOCALLY SOURCED | UNPROCESSED
LASTS FOR CENTURIES
The above list of benefits are great reasons why Light Straw Clay (LSC), is an incredibly effective insulation material for small buildings up to 4 stories tall in almost all climates. Straw coated with clay does not decay, like straw bale can, bugs won't come near it, mold can't grow on it, it's probably fire resistant if not fire proof,
and enjoys tremendous lasting power.
Building with straw and clay for insulation has always been a great option for almost any climate, from Chicago to Cape Comorin, but when
1990's builders and architects in
Germany and the U.S. modernized the mix,
they verified its adaptability to modern life
They collaborted with universities on material testing and to
create standards for its use when writing the IRC definition for it
(IRC Appendix AR).
The door for the average American builder to use LSC opened when one of the world's most knowledgeable architects working with this material, Lou Host-Jablonski, developed a method to couple it with 2x6 framing.
Lou sized the equipment to fit in an average pick-up truck
To use LSC effectively,
we need to streamline its installation process
and
create standards for its use,
by promoting its widespread use,
we are helping the world
future-proof

Locally sourced raw materials are abundantly available
STRAW + CLAY = LIGHT STRAW CLAY
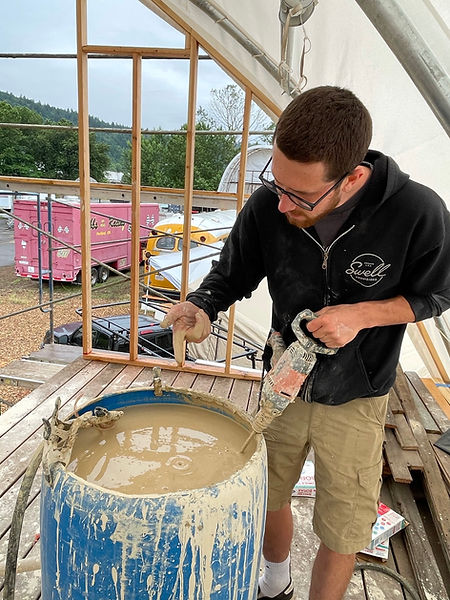
CLAY SLIP: warehouse where Placecraft mixes their slip to bring to the jobsite
Stray is coated with a thin clay slip (clay and water whipped at high speeds), in a specially made tumbler at the jobsite and packed into forms on the 2x6 walls. It is a messy business that involves a short burst of lots of people at the jobsite. The process must be streamlined to appeal to an average, ecologically minded builder. In the meantime, finding an experienced contractor is entirely dependent on the location.
If you are in
New Mexico, Wisconsin, Michigan, or Oregon,
you're in luck.
There's an experience practitioner in each of those states and at least five in Oregon.
An outstanding example is the award winning design+build company, Econest, in Ashland, Oregon. Paula Baker-LaPorte, and builder Robert LaPorte operated a school for budding LSC practitioners for more than 20 years. Students paid Econest for hands-on training at the jobsite, where they worked for one or two weeks, depending on the student's interest (one week for LSC, two weeks for LSC and timber framing).
Econest's school has been integral to the continued use of LSC insulation in the U.S. They taught almost all of the LSC practitioners that I interviewed, from Michigan to Oregon. Their school has been scaled down as they approach retirement, leaving a huge gap in their wake.
Who will train the next generation of practitioners?
My clients for a suburban coach house project in Evanston, Illinois, wanted an all natural wall and when we explored Light Straw Clay (LSC) insulation, we found it impossible to find an experienced LSC contractor close enough to make the trip. The only one within 300 miles didn't want to drive 2 hours to the jobsite. This made me realize that if I want to build an all natural wall, I have to advocate for the use of this material and
develop an LSC school to pass the knowledge along.
The new school will use standard 2x6 framing to create an easier access point for the typical American builder. It will include a research branch to welcome innovative uses, such as the LSC blocks that Placecraft is developing, and to perform ASTM testing for the creation of science based standards for its use. It will promote international collaboration so that we can learn from one another and grow.
Moroccan villages made almost entirely of LSC are still performing incredibly well after 500 years. 12th century German timer framed buildings built with "light earth" (or Leichtlehmbau), are standing strong to this day. That's 1,000 years of continued use. These are only two of countless examples.
What can we learn from the Moroccans? Or Germans, Africans, the French, or the Aussies? Lets collaborate!
TUMBLER: Photo from a jobsite; if you recognize it, please email me so I can credit their work.
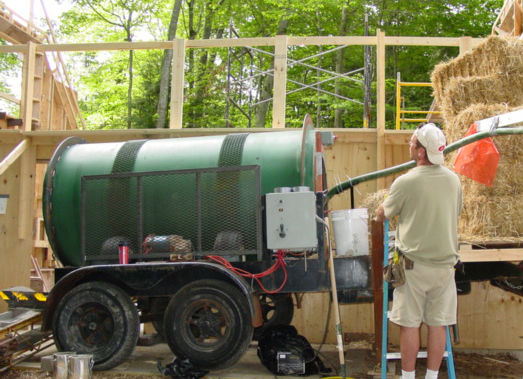
HOW THE WALLS ARE BUILT
Start to finish along the assembly line:
-
whip clay and water at high speeds to create a thin slip
-
toss straw into a tumbler with a thin clay slip
-
slip coats the straw but doesn't make it soggy.
-
the coated straw, or LSC, is carted off via wheelbarrow to the wall,
-
folks stuff the wall cavity with LSC using a pitchfork
-
once stuffed, the plywood forms are moved up a level and filled.
The wall can be stuffed in as quickly as a day,depending on how many volunteers you have and how efficient you are at mixing the straw and clay slip.The process has been likened to a barn raisingand the resulting creation of community is part of LSC's appeal.Kids around 10 years old were optimal wall stuffers at the jobsite I went to last summer.The longer you do this, the better you get at it.I would only build an LSC wall with an experienced contractor.

LSC walls with Larsen truss framing; if you recognize this photo, please email me details to credit the authors.

All in a day's work: stuffing a wall can take from 1-5 days, depending on the number of people at the jobsite on stuffing day.
Plywood is attached to both sides of the wall at the base as forms, the plenum is stuffed with LSC, tamped, and the plywood is moved up for another layer.
​
As contributing author to a reference book underway by Lou Host-Jablonski, I visit existing homes across the country, interviewing the owners, architects, and builders to learn about their process and write about their experience over the years. My contribution to Lou's book will be the precedent studies you see below. My advocacy for the use of LSC grows with every project because the more I learn about it, the more obvious it is that
LSC should be the go-to insulation material for small buildings.
I have yet to meet a person who said they would have built with any other different material if they could have done it over again.
In tandem with highly regarded LSC professionals in the country, I am developing an association that promotes the creation of material standards based on scientific testing and best practice. Scroll down for images of some of the LSC buildings I visited.
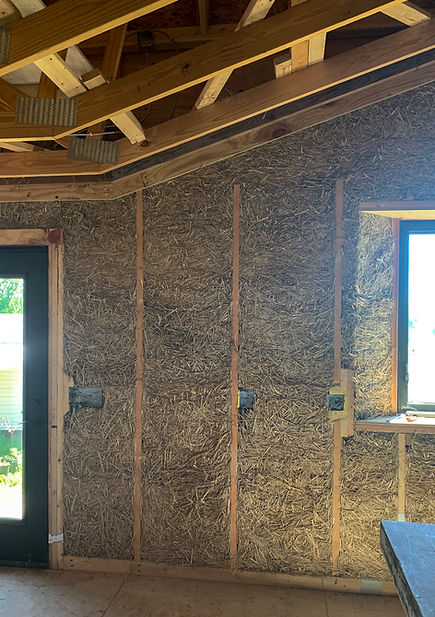
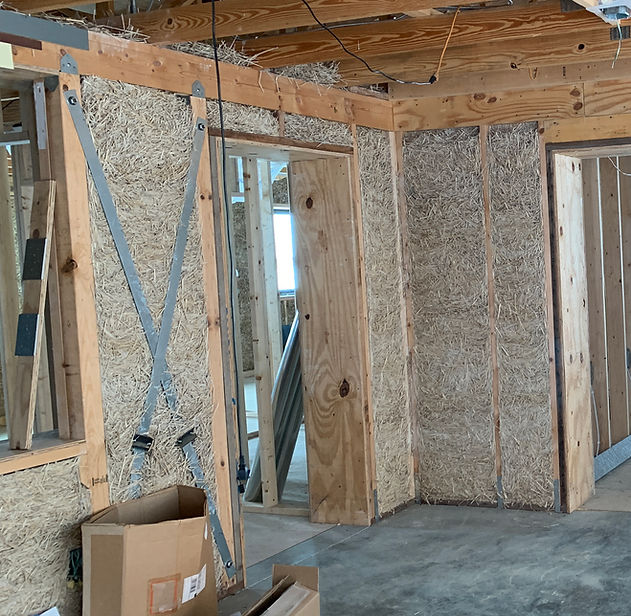
Walls after they are stuffed: note the cross bracing that is used for shear resistance in lieu of plywood sheathing .
Architect: Lou Host-Jablonski Contractor: Jim Hutchison
LIGHT STRAW CLAY INTERIOR WITH 2 x 6 WALL FRAMING,
This innovative construction technique makes LSC accessible to the typical American builder
-
2x6 standard framing with 2x12 bottom and top plates to accommodate the 12 inch thick LSC material
-
Face of 2x6 wall is toward exterior to provide support for future exterior finish application if desired
-
Framing is doubled at kitchens to provide support for cabinets
-
Typical interior finish is plaster, exterior finish can be lime plaster or wood; plaster finish promotes truly breathable walls
LSC PRECEDENTS: MIDWEST TO THE WEST COAST
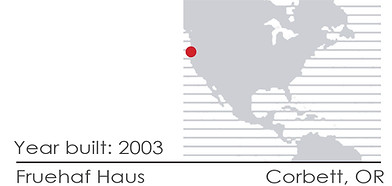
Architect: David Yarborough
Builder: Hammer and Hand
Oregon precedent
Single Family Home
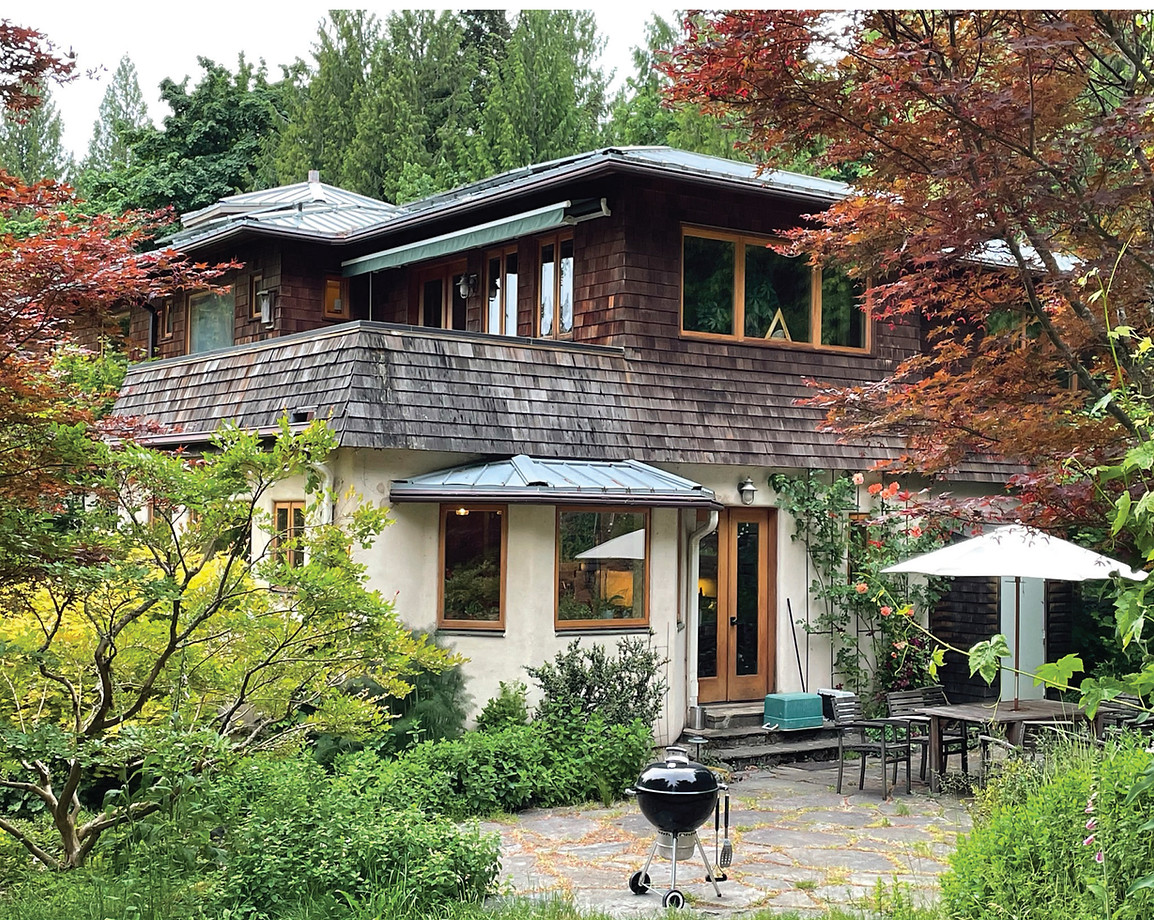
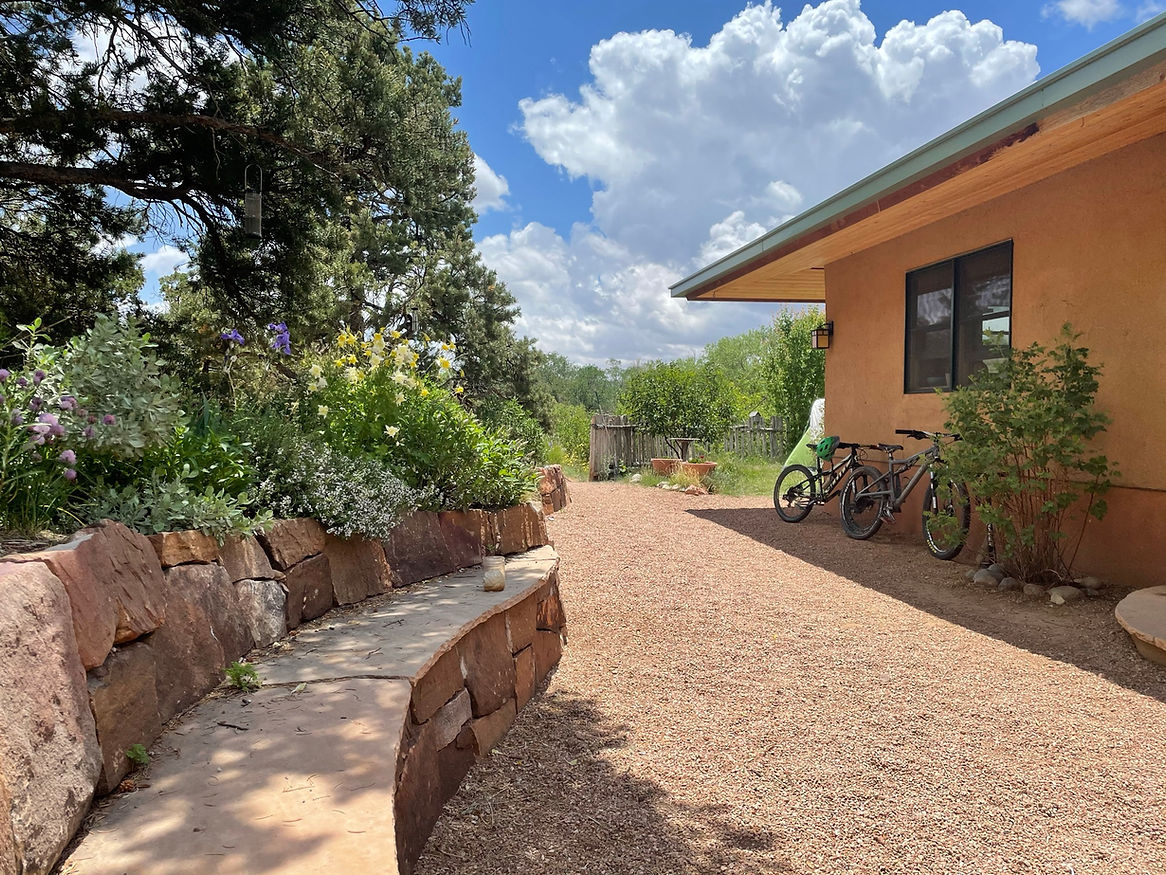
home by Scott Cherry, owner of Lightfoot Construction

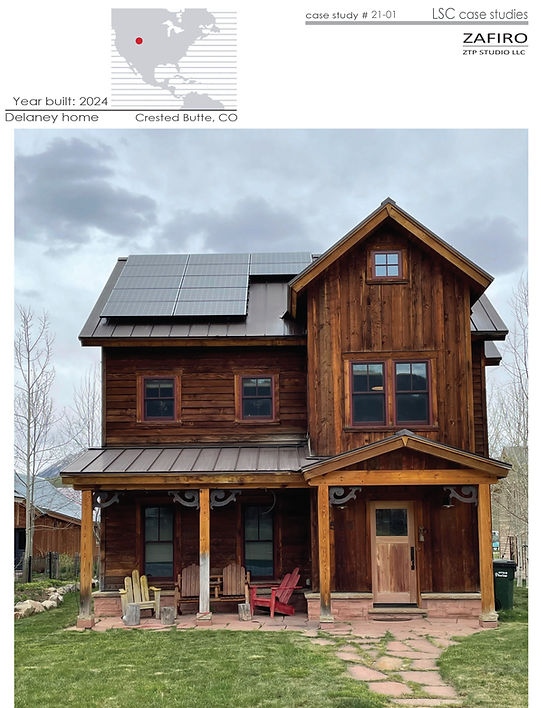
Architect: Multiple
Builder Lydia Doleman

Architect
Builder Don Smith
Colorado House
Oregon Brewery




Designer + Builder:
Lightfoot, Scott Cherry
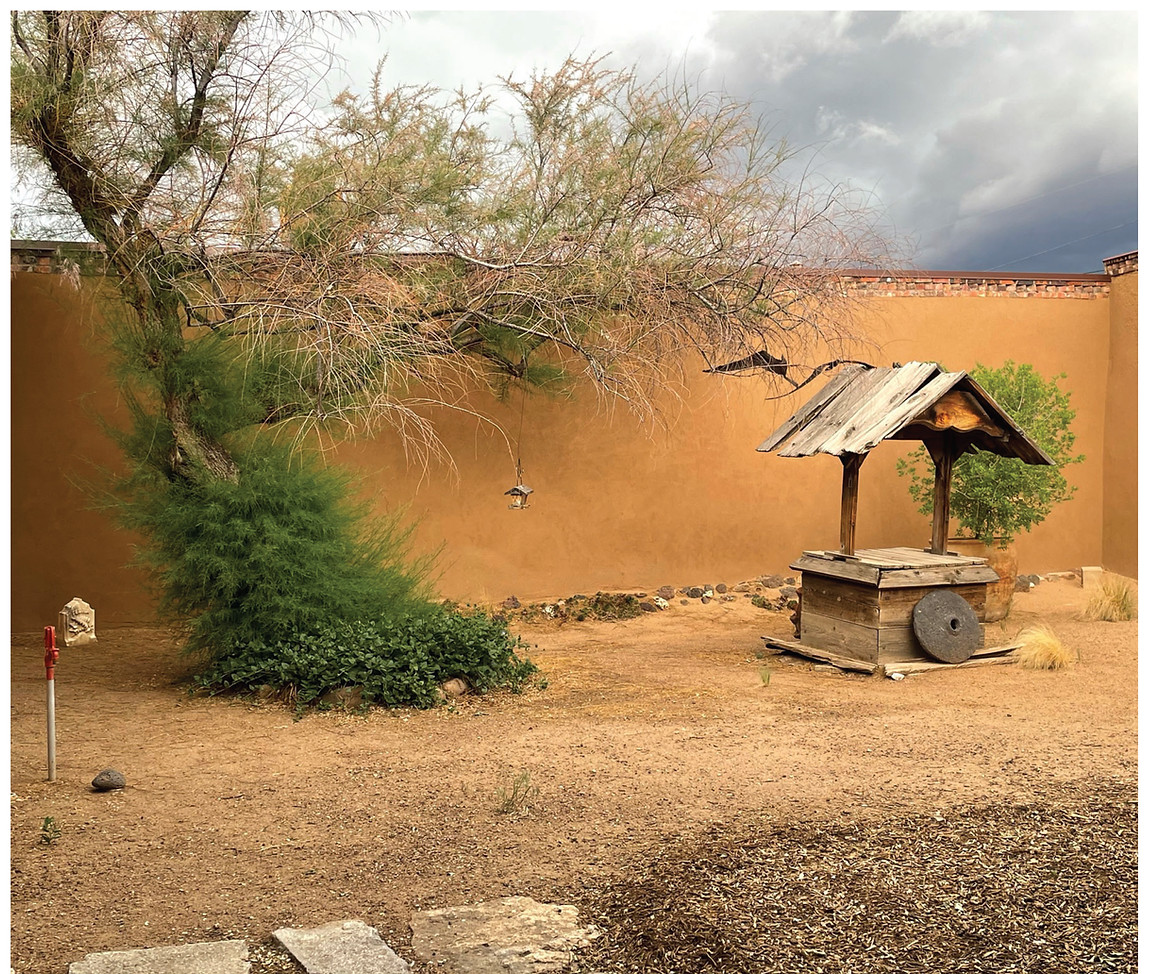

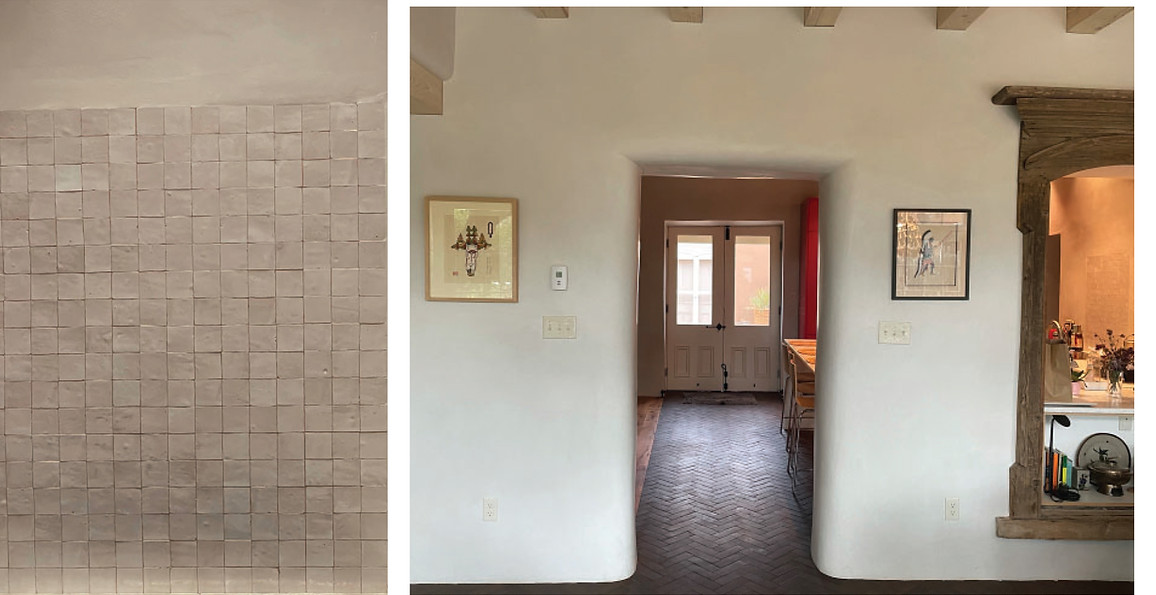




Masonry Stove
Architect: Paula Baker-LaPorte
Builder: Econest, Robert LaPorte
Owner: Paula + Robert
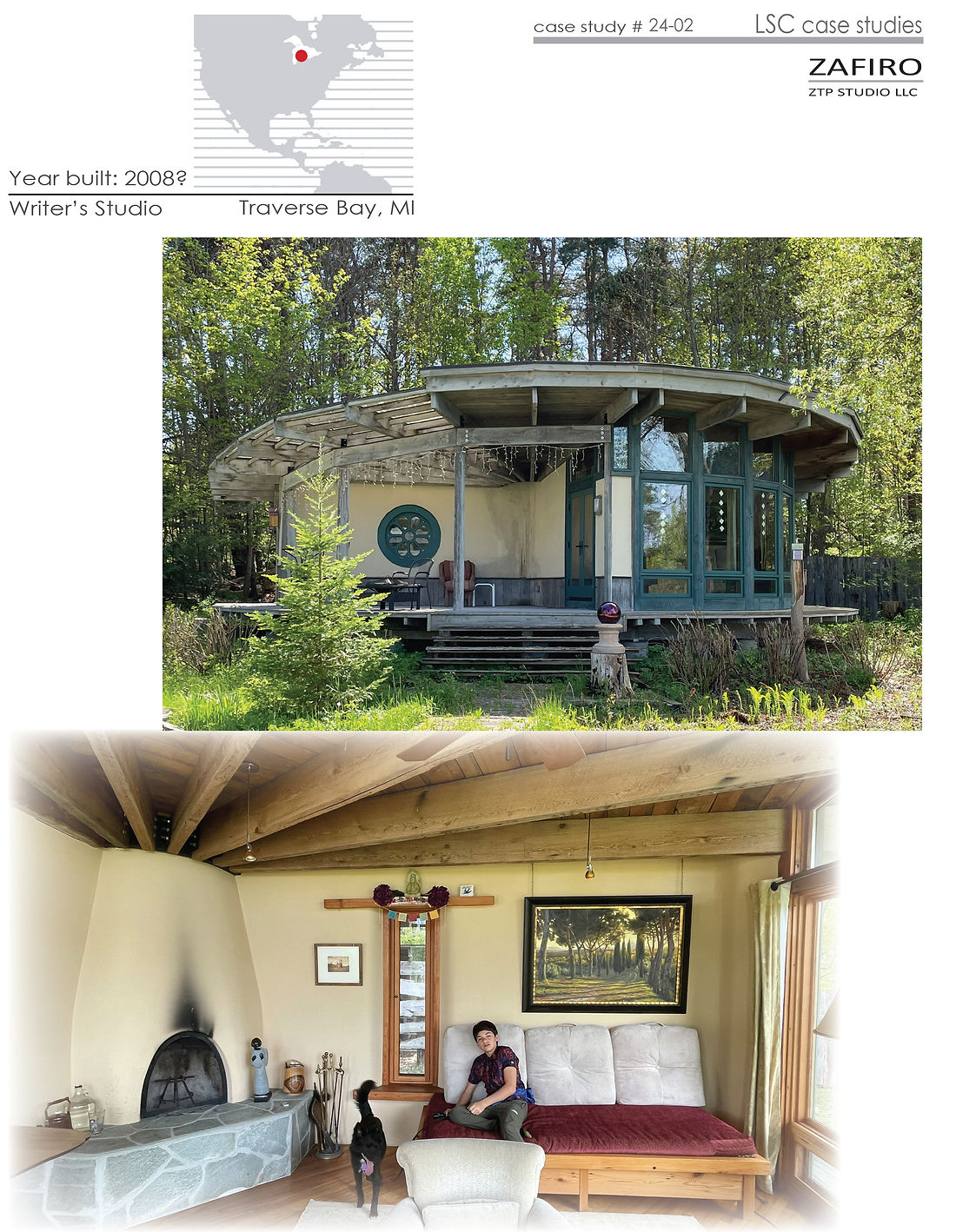
Architect:
Builder: Thomas Hirsch, Bungalow Builders

Architect:
Builder: Thomas Hirsch, Bungalow Builders
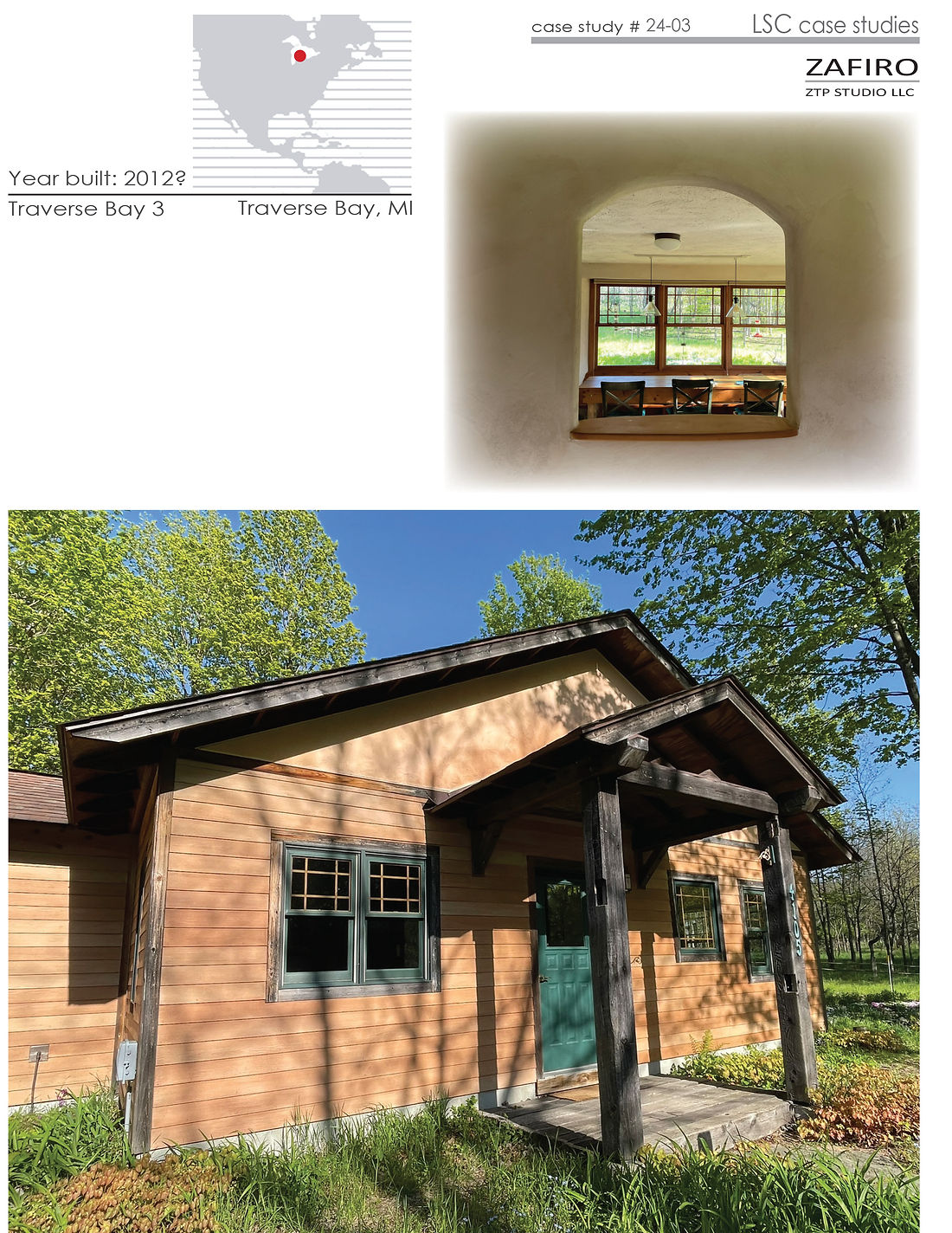
Designer + Builder:
Thomas Hirsch, Bungalow Builders
Designer + Builder: Thomas Hirsch,
Bungalow Builders



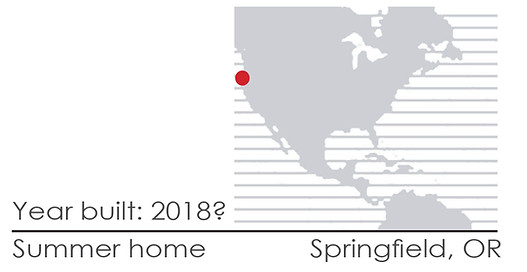
Architect: Erica Ann Busch
Builder: Erica Ann Busch
